+Contract Medical Equipment Manufacturing
26+ Years of Medical Contract Assembly Expertise

Trusted ISO 13485 Certified & FDA Registered
Medical Device Manufacturer
With over 26 years of industry experience, we are an ISO 13485-certified and FDA-registered medical device manufacturer specializing in precision, reliability, and excellence in contract manufacturing.
We provide end-to-end manufacturing solutions for Class I and Class II medical devices, tailored to meet your specific requirements.
Focused on High-Mix, Low-Volume (HMLV) production, our advanced facilities and expert team are equipped to handle complex manufacturing challenges with agility and precision. Our customizable assembly processes are designed to accelerate your time-to-market while maintaining the highest quality standards.
Partner with us to bring your innovative medical devices to life—efficiently, reliably, and with uncompromising quality.
EXECUTIVE SUMMARY
Our Expertise: Accelerating Time-to-Market
Flexible Services: We accept subsystems or complete system assemblies and are adaptable to consignment or turnkey material models. Additionally, we offer options for build-to-order, build-to-stock, and configure-to-order.Highly Qualified and Experienced Team: Our SVP of Engineering and SVP of Manufacturing each bring over three decades of expertise in electronics contract manufacturing, having held key positions at Solectron, Fine Pitch, and Sparqtron. Our passionate and dedicated team excels in custom medical device contract manufacturing, design review, development, prototyping, and assembly of complex medical equipment.Regulatory Compliance: As an ISO 13485 certified and FDA registered manufacturer, we ensure that all products adhere to stringent regulatory standards, including FDA, ISO 13485, ISO 9001, UL, and CE requirements.Complex HMLV Medical Device Assembly: We specialize in outsourced medical device contract manufacturing, particularly in high-mix, low-volume (HMLV) environments, which are essential for precision medical devices.SAP ERP System for Material Management: We have the most qualified and experienced supply teams in both the USA and Taiwan working with our supply chain. By engaging in early material planning with our customers, we proactively address potential supply issues. Our component engineers help customer in cost reduction and source alternative parts. Our use of the SAP ERP system allows us to effectively manage supply and demand, ensuring smooth operations and timely deliveries.Advanced PCB Assembly: Our capabilities include mission-critical Printed Circuit Board Assembly (PCBA) and Circuit Card Assembly (CCA) for medical devices. Our state-of-the-art equipments are equipped to handle precision medical medical assembly and high-mix, low-volume (HMLV) production, ensuring rapid turnaround times for even the most complex devices.Accelerating Time-to-Market: We offer early product development planning, DFM design review, rapid prototyping, and new product introduction (NPI) services, enabling you to bring products to market swiftly.Consistent Quality and Timely Delivery: We view our employees as partners, resulting in a stable workforce with a remarkably low attrition rate. This stability is crucial for consistently delivering high-quality products on time consistantly, with no surprises.Comprehensive Traceability System: Our electronics Manufacturing Execution System (MES), combined with real-time barcode data collection, enhances quality control, ensuring full traceability and regulatory compliance.Offshore Low-Cost Assembly: We have adequate capacity at our Fremont, CA assembly facility, and our Taiwan assembly facility offers an excellent option for cost-effective high-volume production.Proven Success Record: Our extensive client base, including Fortune 500 companies and innovative startups, relies on our unwavering commitment to quality and speed. Many of our clients have been long-term partners, with relationships spanning over five years.
Our Experience in
Advanced Medical Equipment Manufacturing
Medical Laser Photocoagulator
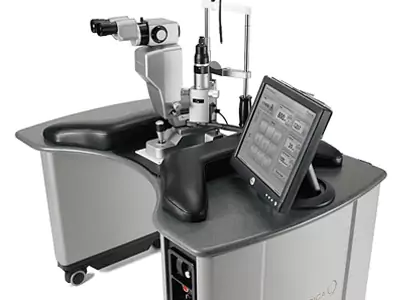
Dual Wavelength
Laser System
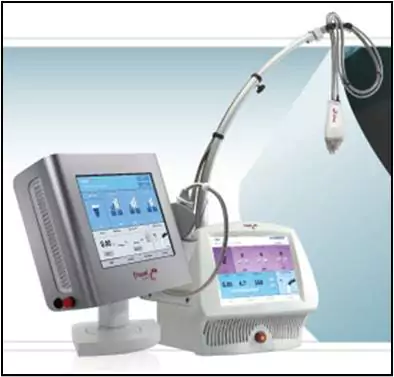
Glaucoma Laser System
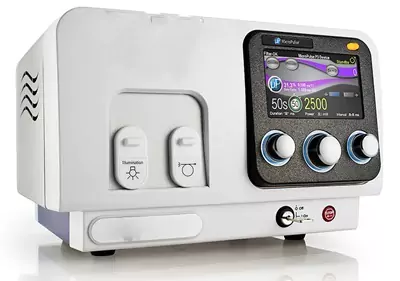
Robotic Hair
Transplant System
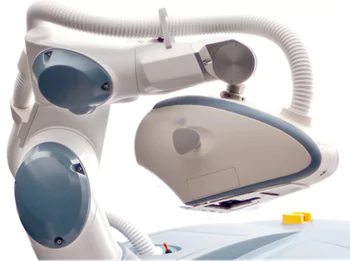
Success Story:
Building a Highly Sophisticated and Complex Medical Equipment
This medical device system comprises over 1,600 parts and involves a very complex process. It also requires an extremely high degree of precision.
Fat Freezer
Sculpting Device
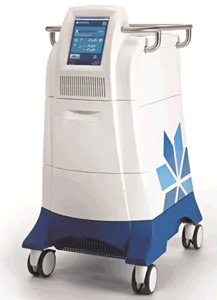
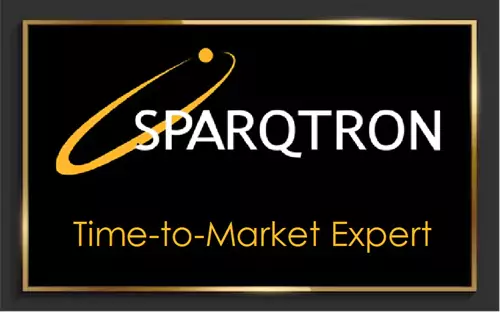
Contact Us today to learn more about how our expertise can accelerate your medical device development.
▲ Back-toTop
Reliable Medical Equipment Manufacturing Services
Our Highly Qualified and Experienced Expert Team:
Our SVP of Engineering and Manufacturing brings over 30 years of experience in the electronics contract manufacturing industry. They have been a pioneer in quick-turn PCB (Printed Circuit Board) prototyping and New Product Introduction (NPI), previously leading global NPI operations at a top tier EMS vendor. Their expertise ensures the seamless integration of new products into manufacturing, a key factor in accelerating time-to-market for innovative electronic products.
Thanks to the wealth of best practices they have developed, we are recognized as leaders in quick-turn PCB prototyping and NPI. Our accuracy and efficiency have earned us a stellar reputation among engineers in Silicon Valley, the global hub of technological innovation.
Contact Us today for a free consultation on how we can help bring your products to market faster.
Success Story - Saving a Medical Distributor's Business:
A medical distributor from China reached out to us for help with their bone density testing equipment, which is their main business and highly successful in China. The original manufacturer of this product had gone out of business, leaving only the CFO available to assist. With the CFO's help, we obtained the necessary product documentation for our study. He also referred us to a technician who used to assemble the system.
Our competent engineers, along with the technician, spent considerable time investigating the issue. Ultimately, we were able to manufacture the product without any problems. We are very pleased to have played a role in saving this business and helping it continue to thrive.
Product Design and Development Support:
We collaborate closely with clients to understand product requirements and specifications. We assist with medical device engineering services, from initial concept through to final design, ensuring manufacturability and regulatory compliance.
Patient-centric design: "Patient safety is our top priority. We provide design review to our client for designing and manufacturing quality medical devices with the utmost consideration for patient well-being."
Do It Right the First Time (DFM, DFT):
We do DFM (Design for Manufacturing) into the early stages of the process to Prevent the need to rework elements later in the process. We make them fit with manufacturing realities, minimize costs because issues can be dealt with early without double-work.
Our engineering support for pre-design for manufacturability (DFM) services ensures that design issues are addressed early, reducing the need for costly revisions during prototype builds. We also provide post-DFM services to minimize manufacturability challenges in future production.Read more ▶
Process Development:
We define manufacturing processes, including equipment and machinery requirements, establish quality control parameters, and develop detailed process documentation to ensure consistent, high-quality production.
Material and Supply Chain Management:

- The Importance of Materials in Medical Devices: Materials play a critical role in the success of medical devices, often accounting for over 70% of the total product cost. A strong supply chain with stringent vendor quality control is essential to maintain profitability and competitiveness.
- Strategic Sourcing and Cost Optimization: We manage the medical device supply chain by sourcing high-quality materials from approved suppliers. Our Far East procurement team ensures cost optimization, while our component engineers identify alternative parts to address lead-time challenges and reduce material costs, helping clients manage expenses efficiently.
- Leveraging Advanced ERP Systems for Supply Chain Management: SAP ERP System allows us to effectively manage supply and demand, ensuring the highest material quality and availability. This ensures smooth operations and timely deliveries, making us a reliable partner in medical device manufacturing.
Manufacturing Process:
We offer a wide range of medical device assembly services, including:
- Printed Circuit Board Assemblies (PCBAs): Using surface mount technology (SMT) or through-hole technology (THT), we solder components onto PCBs.Read more ▶
- Sheet Metal Fabrication and Welding: To cut, bend, and shape thin metal sheets to create various components.
- Injection Molding of Plastic Parts: To produce precise, repeatable plastic components through injection molding.
- Man-Machine Interface (MMI): To design and integrate user interfaces, such as buttons, LED indicators, and touchscreens, for medical devices.
Medical Device Quick-Turn Prototyping:
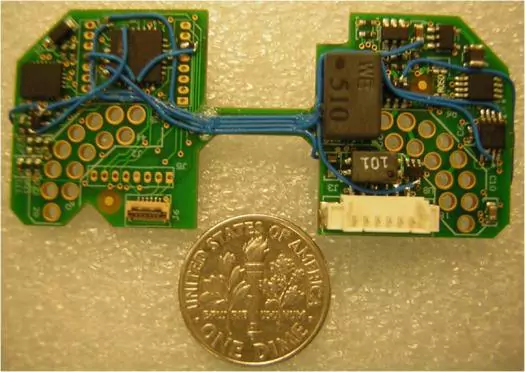
- Importance of Quick-Turn PCB Assembly for Prototyping: Quick-turn PCB assembly (PCBA) prototypes play a crucial role in expediting product development and reducing time-to-market. We offer DFM/DFT engineering services to ensure the prototype is done right the first time. Our quickest turn for PCB assembly prototypes is within 24 hours.Read more ▶
- Skilled Engineering Support for Prototype Reworking: Our engineers and technicians are very skilled in reworking prototypes to avoid the respinning of the PCB design; it saves cost and time to prove the prototype design. This is extremely crucial when there is a tight project schedule.
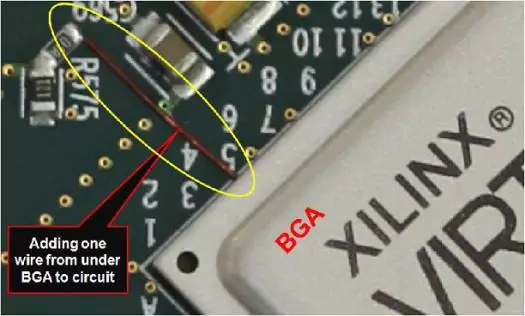
- Success Story of Rapid Prototype Reworking: There was a case where the customer didn't have time to respin the prototype PCB. We helped to add 26 jumper wires to both sides of an extremely small board to make the prototype functional. It helped the customer to show the new product at the trade show with great success.
- Success Story of adding wire from "under BGA" to a circuit: This task is used to change a circuit path at a BGA site for engineering changes/modifications. This process requires precision equipment and highly trained technicians.
New Product Introduction (NPI):
New Product Introduction (NPI) is a critical process that bridges the gap between product development and mass production of medical equipments. We have a a well-defined NPI process to identify potential issues earlier, streamlining process for mass production, cost optimization, and quality assurance.Read more ▶
Devices Verification
Verification is a crucial process in the development and manufacturing of medical devices, ensuring that the device is built correctly according to design specifications. So that the devices are safe, effective, and meet regulatory standards.
Testing: We utilize state-of-the-art testing equipment to perform rigorous functional and performance testing on every device we manufacture. This ensures each product functions flawlessly before reaching patients. Read more ▶
Packaging and Labeling:
We apply clear, accurate product labels and package products according to regulatory requirements and customer specifications. Read more ▶
Medical device Quality Assurance (QA):

Regulatory Compliance: We ensure that all processes adhere to ethical standards and comply with relevant medical device regulations (e.g., FDA, ISO 13485, UL, CE) and regularly update our compliance procedures in meeting the highest safety and quality requirements for patient well-being.Read more ▶
Structured Methodology: Our quality control methodology is designed to ensure the highest levels of safety, effectiveness, and reliability for medical devices. This includes thorough material inspections, controlled manufacturing processes, and comprehensive testing, which are crucial for medical device assembly and manufacturing.
Traceability and Transparency: We maintain a comprehensive traceability system that allows us to track every component and material used in each device. This ensures we can quickly identify and address any potential quality issues. We dedicated to manufacture medical equipment meeting the quality standards and preventing defects and recalls while safeguarding patient safety. We maintaimaintains medical device history records (DHR) in accordance with the requirements of the FDA regulations. Our Quality System ensures that DHR's are maintained in accordance with the Device Master Record (DMR).
Computerized Manufacturing Execution System (MES), coupled with real-time barcode data collection, to track the movement of components and products throughout the manufacturing process. It enhances quality control and ensures traceability and regulatory compliance per medical regulations, such as unique device identification (UDI), etc. We customize our traceability system to meet specific customer needs for medical device and equipment manufacturing.
Continuous improvement: "We are committed to continuous improvement in our quality control processes. We regularly evaluate and update our procedures to ensure we remain at the forefront of medical device safety"
Regular Quality Review Meeting: We conduct regular quality meetings with our OEM customers to ensure we consistently meet their requirements and enhance their satisfaction. During these meetings, we review the mutually agreed-upon KPIs to drive continuous improvement.
Distribution of Medical Equipment:
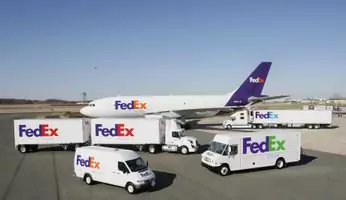
We coordinate with logistics providers for efficient product delivery to the designated locations, manage inventory, and optimize distribution channels to reduce costs and speed up time-to-market for medical equipment manufacturing.
After-sales Support:
It is a critical aspect of the services we provide to our customers, including repair, warranty services, technical support with troubleshooting, spare parts management, handling returns, repairs, and refurbishments, etc.
Sustainability:
We implement environmentally friendly practices, such as waste reduction and energy conservation, and source materials from sustainable suppliers when possible.
Option for Offshore Medical Device Manufacturing:
We have adequate capacity at our Fremont, CA assembly facility, and our Taiwan assembly facility offers an excellent option for high-volume products. We provide competitive offshore manufacturing services at our Taiwan facility, enhancing our clients' competitiveness and helping them capture a larger market share. Taiwan boasts exceptional supply chains for electronic products, further supporting our high-quality manufacturing capabilities.Read more ▶
🤝 Customer Support and Collaboration
We assign dedicated Customer Focus Team (CFT) to assist you at every stage of your project. From initial consultation to final delivery. Our CFT team works closely with you to proactively understand your unique requirements, help you well-plan your projects early, and provide tailored solutions. Our collaborative approach ensures seamless communication and successful project outcomes.Read more ▶
We have a culture of continuous improvement and are always open to your feedback and suggestions. Your opinions are very important to us.
🤝 Your Trusted Partner in Medical Equipment Manufacturing
Developing a lasting partnership in medical device manufacturing goes beyond typical manufacturing relationships. It's built on shared goals, values, and a long-term vision for success. As your strategic partner, we invest in your success by providing comprehensive support that extends beyond production.
Our unwavering commitment to excellence in precision medical equipment assembly has established us as a preferred vendor in the industry. We pride ourselves on delivering:
- Unmatched quality
- Rapid turnaround
- Responsive service
- Consistent results
With our proven track record, we have confidence in meeting your manufacturing needs with precision and efficiency. Count on us as your trusted partner for all your medical device manufacturing requirements.
Request a free consultation!Medical Device Contract Manufacturing Q&A
What is medical device contract manufacturing?
Medical device contract manufacturing is the process where an Original Equipment Manufacturer (OEM) of medical devices outsources various aspects of the manufacturing process to a third-party company.
What are the benefits of contract manufacturing for medical devices?
Benefits include increased production capacity, reduced time to market, improved quality control, access to specialized equipment, and cost-effectiveness.
What should I look for in a contract manufacturer?
Consider their proven experience, quality assurance systems, technological capabilities, communication efficiency, and adherence to medical regulations.
How does contract manufacturing impact time-to-market?
Contract manufacturers can accelerate production, reducing lead times and getting your product to market faster.
What about quality control in contract manufacturing?
Contract manufacturers typically have robust quality control procedures. Look for ISO 13485 certification to ensure compliance with safety and performance requirements.
Can contract manufacturers assist with design?
Yes, contract manufacturers have experienced engineers who can assist in DFM and DFT during design, prototyping, and mass production stages.
Is flexibility important in contract manufacturing?
Absolutely. Contract manufacturers offer flexibility—scaling production up or down based on demand.
How do I ensure efficient communication with a contract manufacturer?
Choose a contract manufacturer with transparent communication channels and a data-driven culture.
What about technological capabilities in contract manufacturing?
Contract manufacturers should have state-of-the-art equipment and resources to handle your specific medical device.
Is cost-effectiveness a factor in contract manufacturing?
Yes, outsourcing can be more cost-effective than building your own manufacturing infrastructure.
Leading Medical Equipment Manufacturing Company
with Oustanding Engineering & Manfacturing Support
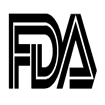
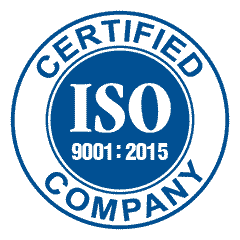
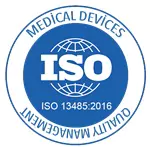
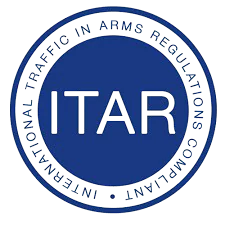
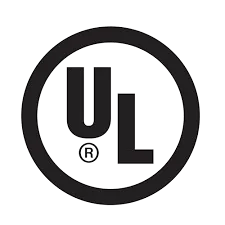
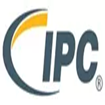
Contact Information: Sparqtron Corporation
Tel: 1-510-657-7198 EXT. 200, eMail: info@sparqtron.com
Address: 5079 Brandin Court, Fremont, California CA 94538, USA
(In Silicon Valley, San Francisco Bay Area, near San Jose, California)